Sure, everybody loves their rugged beauty, but what is the energy efficiency of log homes? How can a stack of logs keep out the cold? Won’t I be wasting my hard-earned cash trying to keep this house warm? A good resource is the Thermal Bypass Checklist Guide put out by Energy Star.
R-Value
First a little bit about R-values. The R-value of a material refers to its resistance to heat flow and was adopted in the 1970s during the first energy crisis as a simple way to compare energy efficiency.
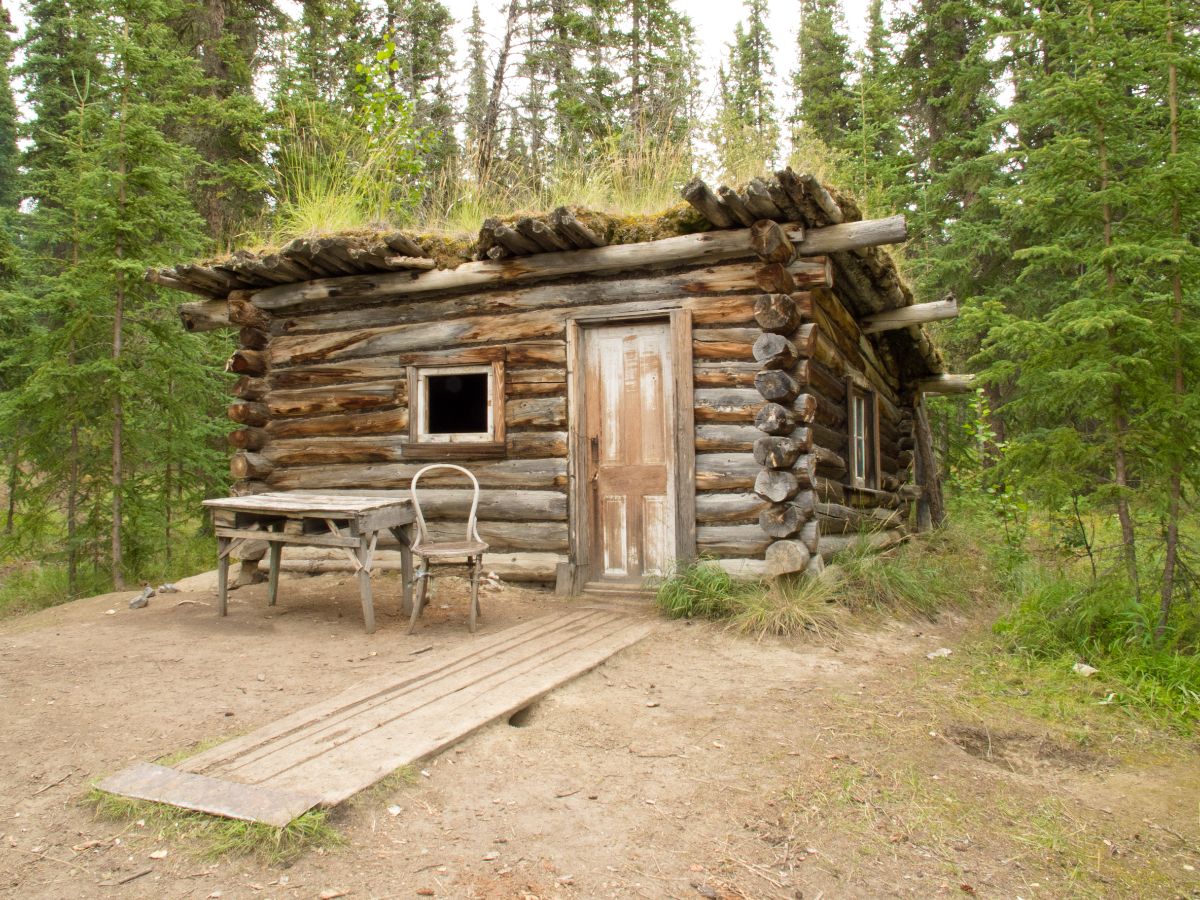
So we commonly see R-value ratings for things like fiberglass batt insulation, where:
- 3 ½” (2 x 4 wall) is rated at R-13
- 5 ½” (2 x 6 wall) is rated at R-19
But in the laboratory where they do the rating, the fiberglass batt is actually enclosed in plastic, completely stopping any air flow (unlike the real world) and the difference in temperature that is measured is only 10 degrees (again, vastly different from comparing outside and inside temperatures of a house in New England in the winter, for example, where the temperature differential might be 70 degrees or more).
This is a complex issue that cannot be reduced to one simple metric such as R-value.
Thermal Mass
Log homes take advantage of what is referred to as “thermal mass” effect, using the heat capacity of the wall. That is, the mass of the solid wood absorbs and holds the heat and slowly releases it over time.
Studies done for the Department Of Energy (DOE) and the Department of Housing and Urban Development (HUD) by the National Bureau of Standards compared energy costs between houses insulated with fiberglass to a value of R-13 and log homes built with 7” thick square logs. They showed that the two homes used the same amount of energy, even though the stick-framed house had a nominal R-value 17% higher.
The energy efficiency of log homes can be as much as 15% better than conventional stick-framed houses.
Prevent Air Infiltration
One very important factor to get right when building log cabins is the prevention of air infiltration. Some of the ways to do this are:
- Sealing between the logs using a ribbon of caulk or foam
- Carefully caulking the corners where the logs come together
- Sealing the windows and doors and other penetrations in the exterior skin with expanding foam or caulk
- Insulating the edge of the concrete (if built on a slab) with, for example, Styrofoam XPS or extruded polystyrene
- Using good insulation in the cabin roof (especially if they are cathedral ceilings)
- Using sill seal between bottom log and foundation and between bottom plates and floor decks
- Providing a clear ventilation path for the roof without exposing a path for interior air (and heat) to escape
- Use the proper log fasteners to secure logs
These are all good ways to boost the energy efficiency of log homes and reduce your monthly energy bill, since the DOE estimates that 44% of your total utility bill pays for heating and cooling of your home. Your log home will feel more comfortable and long-term maintenance will be reduced. Shop Now
More Cabin Efficiency Pages:
Solar Power Saves Money and Resources Both passive solar power and active solar power offer ways to save money along with our planets resources.
Thermal Bypass Checklist Guide The Thermal Bypass Checklist Guide addresses the best practice ways to be qualified as ENERGY STAR.
Log Home Systems – An Integrated Approach Using an integrated approach to log home systems will result in greater efficiency, lower building costs, superior performance and overall savings.
Optimal Value Engineering Optimal Value Engineering is a mindful design process that minimizes waste and increases efficiency.
Thermal Mass Effect of Logs The thermal mass effect of solid logs makes cabins energy efficient.
Steven Altmann
5/9/2022
Dear Sir,
I've always loved log houses and I'm seriously thinking of building one. Living in Connecticut, I've decided on applying passive heating techniques. I require a single level ranch design with an unfinished 10' high unfinished basement. Almost all the "new" construction videos show construction on a slab with foam forms for footings ... and the slab poured with foam between slab and foundation for the thermal break. Fair enough. My first floor is now 10" up and everybody is still using traditional wooden rafters and plywood and minimal attempts at a thermal break. My mind has a cement floor up there with radiant heating ... plus an extra zone or two to take the passive heat away from two vertical masonry walls (plus the floor) and move it to a tank for reuse each evening. There is no way the weight of a cement floor plus masonry, kitchen, furniture, walls etc. can be carried on plywood and wooden rafters. Has anyone thought of an independent structure made of steel columns and rafters and pour a thin concrete floor similar to a second floor of a simple office building? As long as you framed out the staircase and kitchen and bath chases, you would end up with (1) perfect thermal break (2) huge thermal mass (3) you could run PEX till your heart is content. Heck you would probably have so much extra heat, you would have to add-on 2 more zones and heat your garage floor with it !!!
There has to be a better way than nailing zones of PEX to the underside of the first floor plywood. I've come to the conclusion that 1) they are on a slab 2) they made additional foundation walls 3) they have a basement of columns all over the place making the basement unusable for any type of shop.
BTW ... you have an extremely well thought out website. Lots of brain food. It is a rare talent to have an inventory of answers before your client knows the question.